Có nhiều phương pháp làm sạch bề mặt kim loại được áp dụng trong công nghiệp, mỗi phương pháp có ưu, nhược điểm và phạm vi ứng dụng riêng. Lựa chọn phương pháp phù hợp phụ thuộc vào loại kim loại, loại tạp chất, mức độ sạch yêu cầu, điều kiện thi công và yếu tố kinh tế.
Làm Sạch Cơ Học
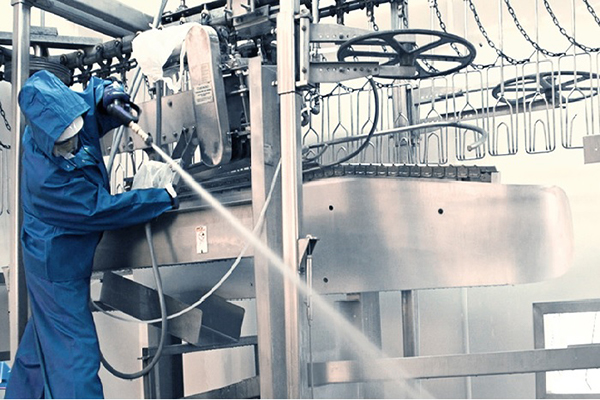
Làm Sạch Bằng Dụng Cụ Cầm Tay và Dụng Cụ Điện:
- Quy trình: Sử dụng các công cụ thủ công (không dùng điện – Hand Tool theo SSPC-SP2 ) hoặc công cụ chạy điện (Power Tool theo SSPC-SP3 , SSPC-SP11 , SSPC-SP15 ) như bàn chải sắt, dao cạo, giấy nhám, máy mài, máy đánh gỉ dạng kim (needle gun) để loại bỏ gỉ sét, vảy cán, sơn cũ bám dính lỏng lẻo.
- Tiêu chuẩn: SSPC-SP2, SP3, SP11 (Làm sạch tới kim loại trần), SP15 (Cấp độ thương mại); ISO St2, St3 (St2: Làm sạch kỹ; St3: Làm sạch rất kỹ bằng cạo/chải ). TCVN 8790 cũng mô tả St2 và St3.
- Dụng cụ: Bàn chải sắt, dao cạo, giấy/đĩa nhám, búa gõ gỉ, máy mài góc, máy đánh gỉ dạng kim.
- Ưu điểm: Chi phí đầu tư ban đầu thấp, phù hợp cho các khu vực nhỏ, sửa chữa cục bộ hoặc những nơi không thể áp dụng phương pháp phun cát , ít yêu cầu che chắn hơn phun cát.
- Nhược điểm: Tốn nhiều công sức và thời gian, hiệu quả làm sạch thấp hơn, thường tạo ra bề mặt không đồng đều, không loại bỏ được các tạp chất bám dính chặt , có thể làm chai (burnish) bề mặt kim loại, giảm độ bám dính , tạo ra bụi và tiếng ồn , có nguy cơ tạo các cạnh sắc, vết xước nếu không cẩn thận. Yêu cầu làm sạch dầu mỡ trước (ví dụ theo SSPC-SP1).
Làm Sạch Bằng Phun Mài Mòn (Abrasive Blast Cleaning):
- Quy trình: Bắn các hạt mài (cát, hạt bi, hạt thép góc cạnh) với tốc độ cao lên bề mặt kim loại bằng khí nén (phun khí nén – air blasting) hoặc bánh văng ly tâm (phun bi – wheel blasting) để loại bỏ tạp chất và tạo ra một bề mặt nhám (anchor pattern).
- Tiêu chuẩn: ISO 8501-1 cấp Sa (Sa 1, Sa 2, Sa 2.5, Sa 3) ; SSPC/NACE SP5/NACE 1 (Kim loại trắng) , SP10/NACE 2 (Gần trắng) , SP6/NACE 3 (Thương mại) , SP14/NACE 8 (Công nghiệp) , SP7/NACE 4 (Phủi sạch). TCVN 8790 cũng định nghĩa các cấp Sa.
- Loại hạt mài: Cát, khoáng chất/xỉ (SSPC-AB 1 ), hạt thép tròn (shot – tạo profile lõm ), hạt thép góc cạnh (grit – tạo profile nhọn ), các loại khác (dây thép cắt, gang cầu). Lựa chọn hạt mài ảnh hưởng đến độ nhám bề mặt. Tiêu chuẩn về độ sạch của hạt mài tái chế SSPC-AB 2.
- Ưu điểm: Rất hiệu quả trong việc loại bỏ các tạp chất bám dính chặt , tạo ra độ nhám bề mặt lý tưởng cho sự bám dính của lớp phủ , tương đối nhanh chóng cho các bề mặt lớn. Được xem là tiêu chuẩn vàng cho nhiều hệ sơn hiệu suất cao.
- Nhược điểm: Tạo ra lượng bụi lớn (phun khô), đòi hỏi hệ thống thu hồi bụi, che chắn và bảo hộ hô hấp nghiêm ngặt , gây tiếng ồn , có khả năng làm hạt mài găm vào bề mặt , nguy cơ gỉ sét nhanh (flash rust) nếu bề mặt bị ẩm sau khi làm sạch , có thể làm biến dạng các tấm kim loại mỏng. Yêu cầu làm sạch dầu mỡ trước (SSPC-SP1).
Làm Sạch Hóa Học
Làm Sạch Bằng Dung Môi (Solvent Cleaning):
- Quy trình: Sử dụng dung môi hữu cơ, nước, chất tẩy rửa, dung dịch kiềm hoặc chất nhũ hóa để loại bỏ các tạp chất hòa tan như dầu, mỡ, bụi bẩn, muối. Các phương pháp bao gồm lau, chải, phun, ngâm, tẩy dầu mỡ bằng hơi (vapor degreasing), làm sạch bằng hơi nước. Yêu cầu loại bỏ các mảnh vụn lỏng lẻo trước và đảm bảo sử dụng dung môi, giẻ lau sạch cho lần cuối.
- Tiêu chuẩn: SSPC-SP1.
- Ứng dụng: Chủ yếu để loại bỏ các chất bẩn hữu cơ; là bước làm sạch sơ bộ bắt buộc trước khi áp dụng các phương pháp khác.
- An toàn/Môi trường: Cần thông gió tốt, trang bị bảo hộ cá nhân (PPE) và tuân thủ các quy định về sử dụng và thải bỏ dung môi. Một số dung môi (TCE, nPB, perc) có thể gây nguy hại đáng kể cho sức khỏe và môi trường.
Làm Sạch Bằng Kiềm (Alkaline Cleaning):
- Quy trình: Ngâm hoặc phun dung dịch nước chứa các chất tạo kiềm (ví dụ: NaOH, KOH, phốt phát, silicat) và chất hoạt động bề mặt (surfactant). Thường bao gồm nhiều bước: rửa kiềm (thường gia nhiệt, có thể kết hợp siêu âm/khuấy trộn), rửa nước, xử lý axit (tùy chọn, để loại bỏ oxit), rửa nước, thụ động hóa (tùy chọn).
- Cơ chế: Xà phòng hóa (biến dầu mỡ thành xà phòng), tẩy rửa (đẩy chất bẩn ra khỏi bề mặt), nhũ hóa (phân tán dầu mỡ), hòa tan.
- Ứng dụng: Loại bỏ các chất bẩn hữu cơ (dầu, mỡ), bụi bẩn, vụn kim loại khỏi nhiều loại kim loại. Lựa chọn chất tạo kiềm phụ thuộc vào kim loại (ví dụ: silicat bảo vệ nhôm ).
- Ưu điểm: Hiệu quả đối với chất bẩn hữu cơ, có thể tự động hóa.
- Nhược điểm: Cần kiểm soát chặt chẽ thành phần hóa học của dung dịch (theo dõi, bổ sung ), việc rửa sạch là tối quan trọng để loại bỏ hóa chất dư thừa , cần xử lý nước thải từ dung dịch đã qua sử dụng.
Tẩy Gỉ Bằng Axit (Acid Pickling):
- Quy trình: Ngâm trong dung dịch axit (thường là HCl hoặc H2SO4 cho thép; HF, HNO3, H3PO4 cho các kim loại khác) để loại bỏ các tạp chất vô cơ như gỉ sét, vảy cán, oxit. Các bước điển hình bao gồm làm sạch sơ bộ (tẩy dầu mỡ), ngâm axit, rửa nước, trung hòa (bằng dung dịch kiềm), rửa nước, áp dụng chất ức chế gỉ (tùy chọn), sấy khô.
- Ứng dụng: Chủ yếu để loại bỏ vảy cán trên thép sau gia công nóng, loại bỏ gỉ sét. Tạo ra bề mặt hoạt hóa, sẵn sàng cho mạ điện hoặc sơn phủ.
- Ưu điểm: Hiệu quả cao trong việc loại bỏ vảy cán/gỉ sét , tạo bề mặt nhám tăng cường bám dính , chi phí tương đối thấp.
- Nhược điểm: Sử dụng axit nguy hiểm đòi hỏi quy trình an toàn nghiêm ngặt (PPE, thông gió) và quy trình xử lý chất thải đặc biệt , nguy cơ tẩy quá mức hoặc gây giòn hydro đối với một số loại thép , không phù hợp với mọi hình dạng sản phẩm hoặc ứng dụng tại hiện trường.
Tẩy Dầu Mỡ Bằng Hơi (Vapor Degreasing):
- Quy trình: Chi tiết kim loại được treo trong buồng phía trên dung môi đang sôi. Hơi dung môi nóng bốc lên, ngưng tụ trên bề mặt chi tiết kim loại lạnh hơn, hòa tan các chất bẩn (dầu, mỡ, sáp). Dung môi ngưng tụ mang theo chất bẩn chảy xuống đáy buồng. Quy trình thường bao gồm các giai đoạn ngâm, có thể kết hợp với siêu âm.
- Ứng dụng: Làm sạch các chi tiết phức tạp có khe hẹp, lỗ sâu, chuẩn bị bề mặt cho các công đoạn hoàn thiện. Hiệu quả với các chất bẩn không tan trong nước.
- Ưu điểm: Làm sạch hiệu quả, chi tiết sau khi xử lý sạch và khô , dung môi có thể được thu hồi và tái sử dụng , phù hợp với các chi tiết nhạy cảm với nước.
- Nhược điểm: Chi phí thiết bị ban đầu cao , yêu cầu sử dụng dung môi đặc biệt, không cháy , hơi dung môi có thể độc hại đòi hỏi hệ thống kín và thông gió tốt , có thể gây lo ngại về môi trường tùy thuộc vào loại dung môi.
3.3. Các Phương Pháp Tiên Tiến & Chuyên Dụng
Làm Sạch Bằng Siêu Âm (Ultrasonic Cleaning):
- Quy trình: Sử dụng sóng âm tần số cao (20-400 kHz) truyền qua dung dịch làm sạch (nước hoặc dung môi, thường có chất tẩy rửa) để tạo ra các bong bóng khí nhỏ li ti (hiện tượng xâm thực – cavitation). Sự hình thành và vỡ tức thời của các bong bóng này tạo ra năng lượng cực lớn, tác động như hàng triệu bàn chải nhỏ, đánh bật các chất bẩn khỏi bề mặt, kể cả trong các chi tiết phức tạp và lỗ mù. Thường được kết hợp với làm sạch bằng kiềm hoặc hóa chất khác.
- Ứng dụng: Làm sạch chính xác các chi tiết phức tạp (điện tử, thiết bị y tế, linh kiện ô tô), loại bỏ các chất bẩn bám dính chặt.
- Ưu điểm: Hiệu quả làm sạch cao, làm sạch được các hình dạng phức tạp , nhẹ nhàng với chi tiết , có thể giảm yêu cầu tháo rời chi tiết , nhanh chóng.
- Nhược điểm: Yêu cầu thiết bị chuyên dụng, hiệu quả phụ thuộc vào dung dịch và tần số lựa chọn, có thể gây hư hỏng cho các linh kiện cực kỳ nhạy cảm (ví dụ: thiết bị MEMS ).
Làm Sạch Bằng Tia Nước Áp Lực Cao (High-Pressure Water Jetting):
- Quy trình: Sử dụng tia nước được đẩy đi với áp suất rất cao (đôi khi kết hợp với hạt mài – hydroblasting/phun mài mòn ướt ) để loại bỏ lớp phủ cũ, gỉ sét và các chất bẩn.
- Tiêu chuẩn: SSPC-SP12/NACE 5 định nghĩa các mức độ sạch. Tiêu chuẩn hình ảnh SSPC-VIS 4/NACE No. 7 được áp dụng.
- Ưu điểm: Giảm thiểu bụi so với phun khô , hiệu quả trong việc loại bỏ muối và các lớp phủ dày, có thể tạo độ nhám nếu sử dụng hạt mài.
- Nhược điểm: Bề mặt còn ẩm ướt, cần sấy khô trước khi sơn , có nguy cơ gây gỉ sét nhanh (flash rust) , chi phí thiết bị cao, tiềm ẩn nguy cơ mất an toàn do áp lực nước rất cao. Không loại bỏ được vảy cán bám chặt nếu không dùng hạt mài.
Đề cập Ngắn Gọn Các Phương Pháp Khác:
- Làm Sạch Bằng Ngọn Lửa (Flame Cleaning): Sử dụng ngọn lửa oxy-axetylen để đốt cháy và loại bỏ vảy cán, chất bẩn. Kém hiệu quả với gỉ sét, có thể gây biến dạng kim loại.
- Làm Sạch Bằng Laser (Laser Cleaning): Sử dụng tia laser hội tụ để làm bay hơi hoặc bóc tách chất bẩn khỏi bề mặt. Phương pháp chính xác, sạch sẽ, nhưng thường có chi phí cao hơn và tốc độ chậm hơn cho các diện tích lớn.
Sự phát triển của các phương pháp làm sạch, từ các quy trình thủ công và hóa học đơn giản đến các kỹ thuật tiên tiến như siêu âm và laser, phản ánh nhu cầu ngày càng tăng về mức độ sạch cao hơn, hiệu quả tốt hơn và an toàn hơn cho người lao động cũng như môi trường. Các phương pháp mới thường giải quyết được những hạn chế của các phương pháp cũ (ví dụ: giảm bụi so với phun cát khô, giảm nguy cơ từ dung môi độc hại).
Nhiều phương pháp đòi hỏi sự kiểm soát chặt chẽ các thông số vận hành (ví dụ: áp suất/loại hạt mài khi phun cát , nồng độ/nhiệt độ trong bể hóa chất , tần số/công suất siêu âm ) và thường yêu cầu các bước xử lý tiếp theo (ví dụ: rửa, sấy khô, thụ động hóa ). Sự phức tạp này nhấn mạnh tầm quan trọng của việc có đội ngũ vận hành được đào tạo bài bản và quy trình kiểm soát chất lượng nghiêm ngặt để đảm bảo bề mặt được chuẩn bị một cách nhất quán và hiệu quả.